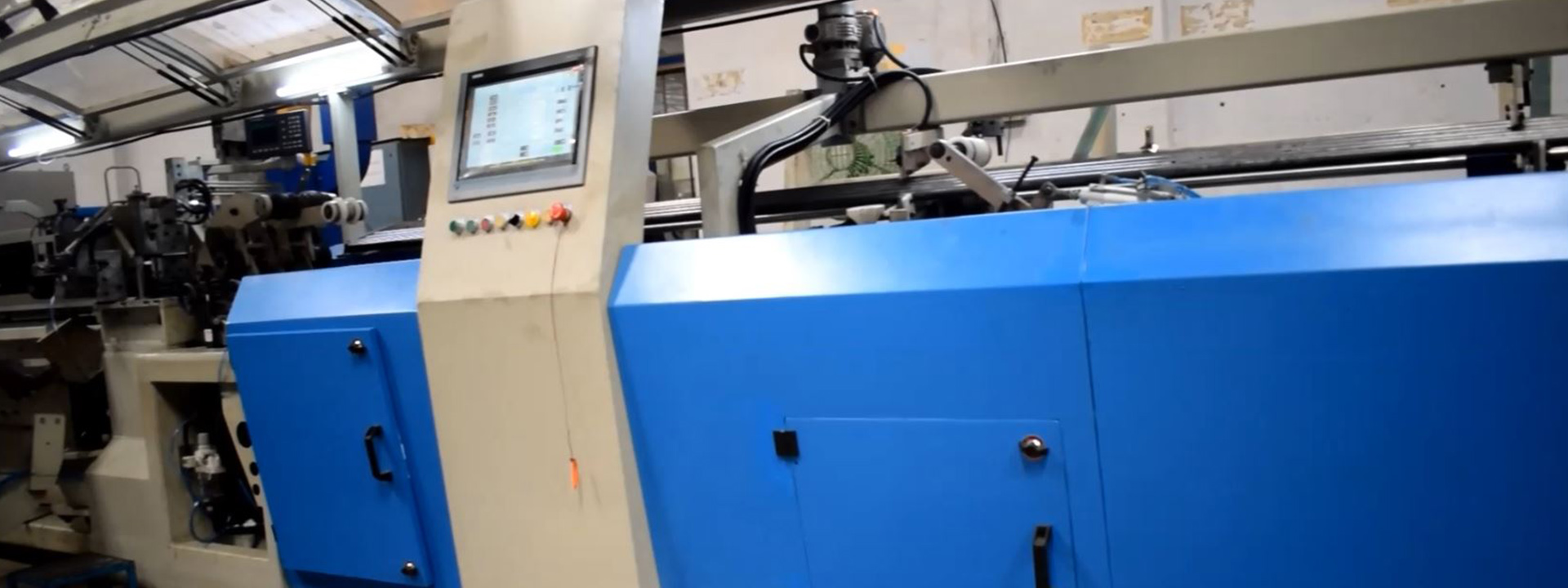
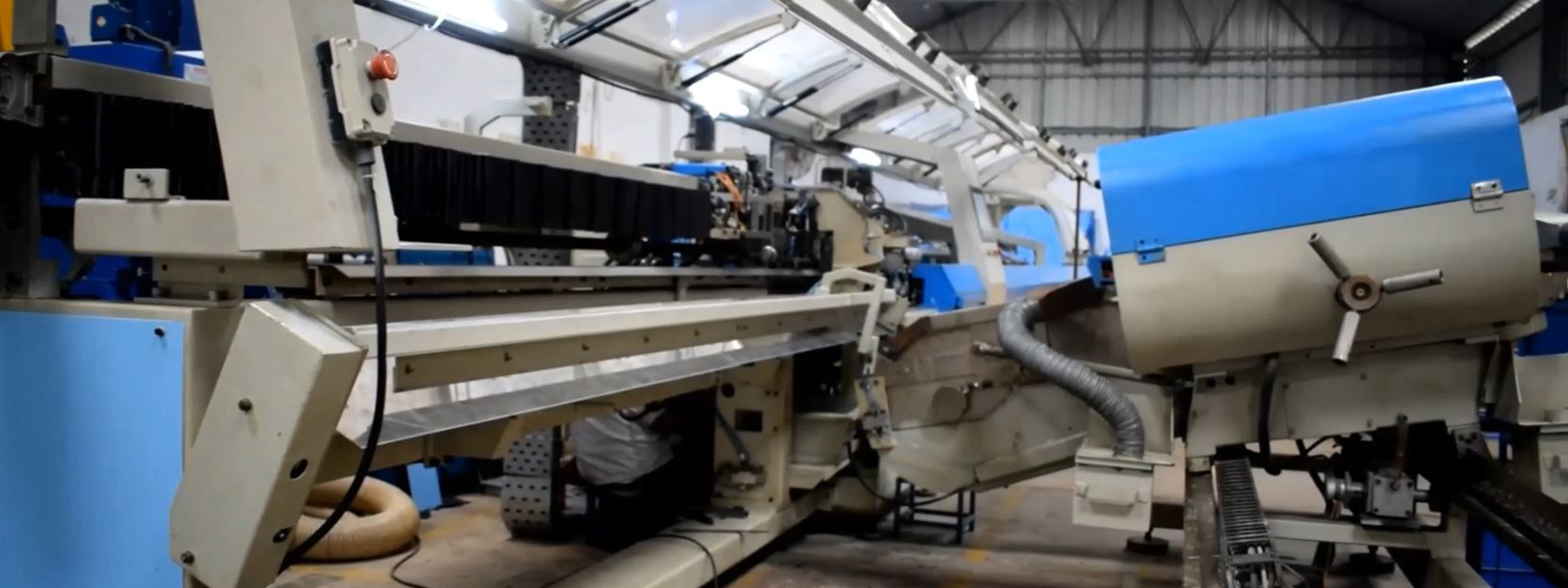
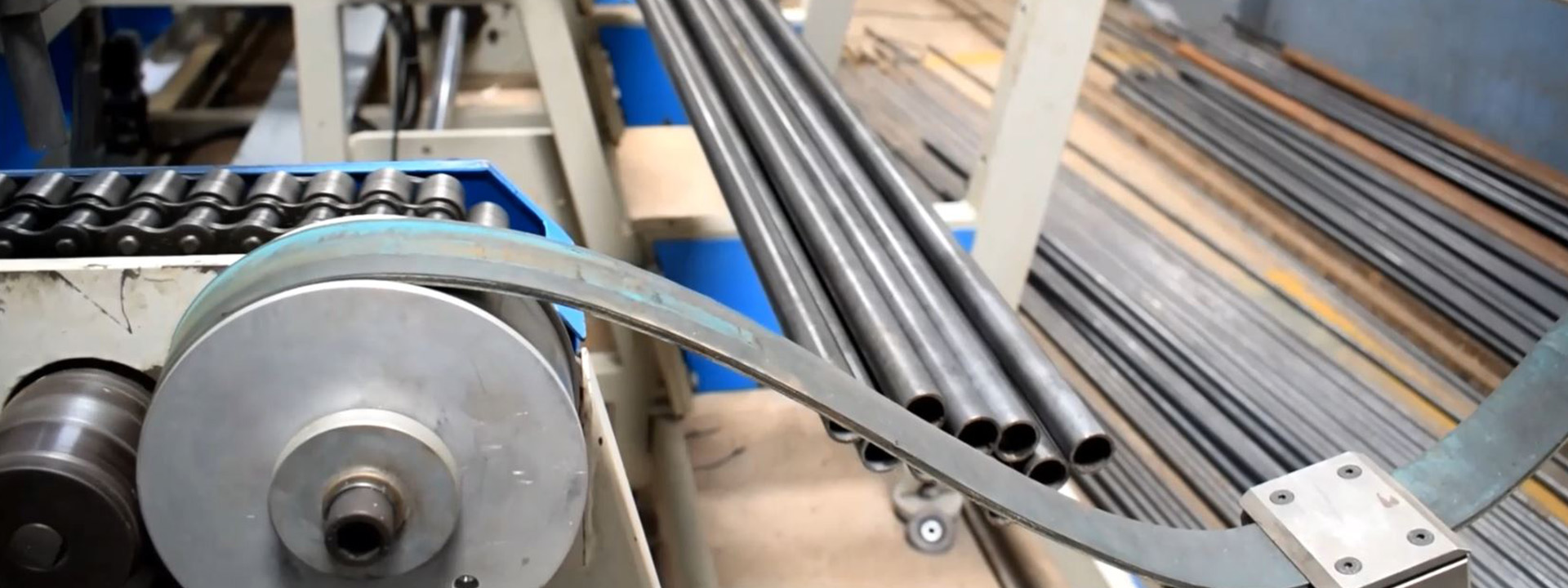
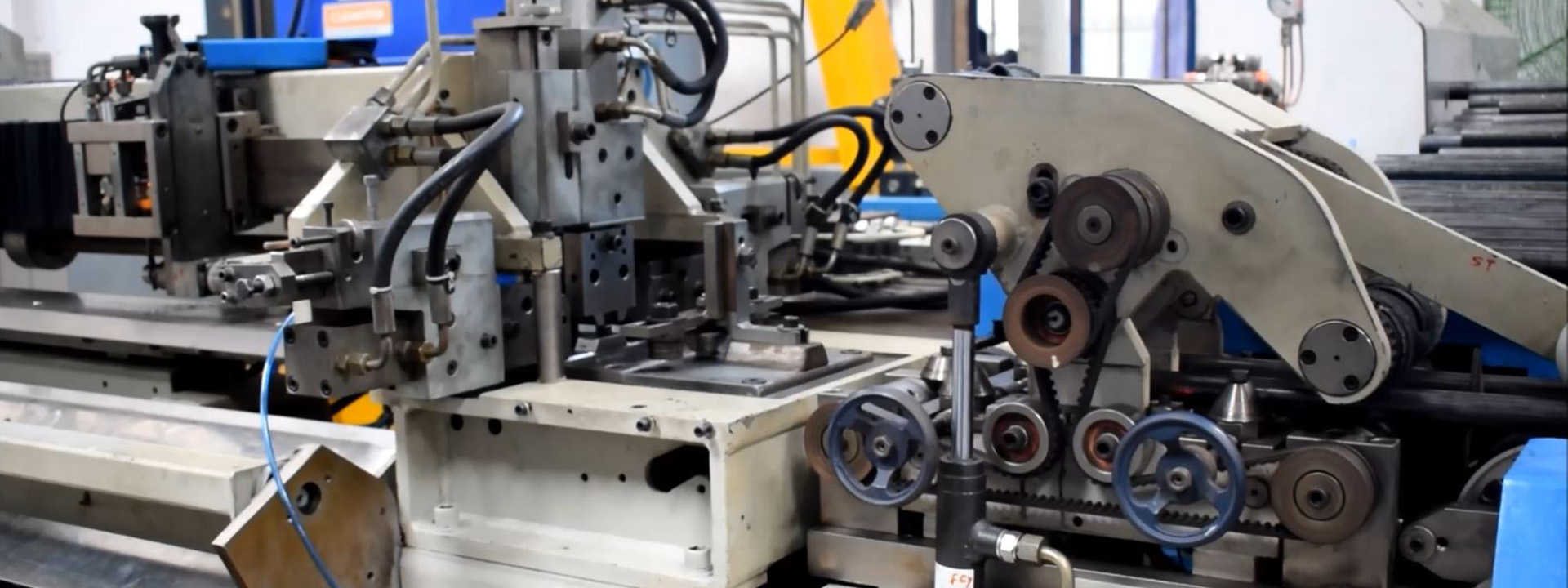
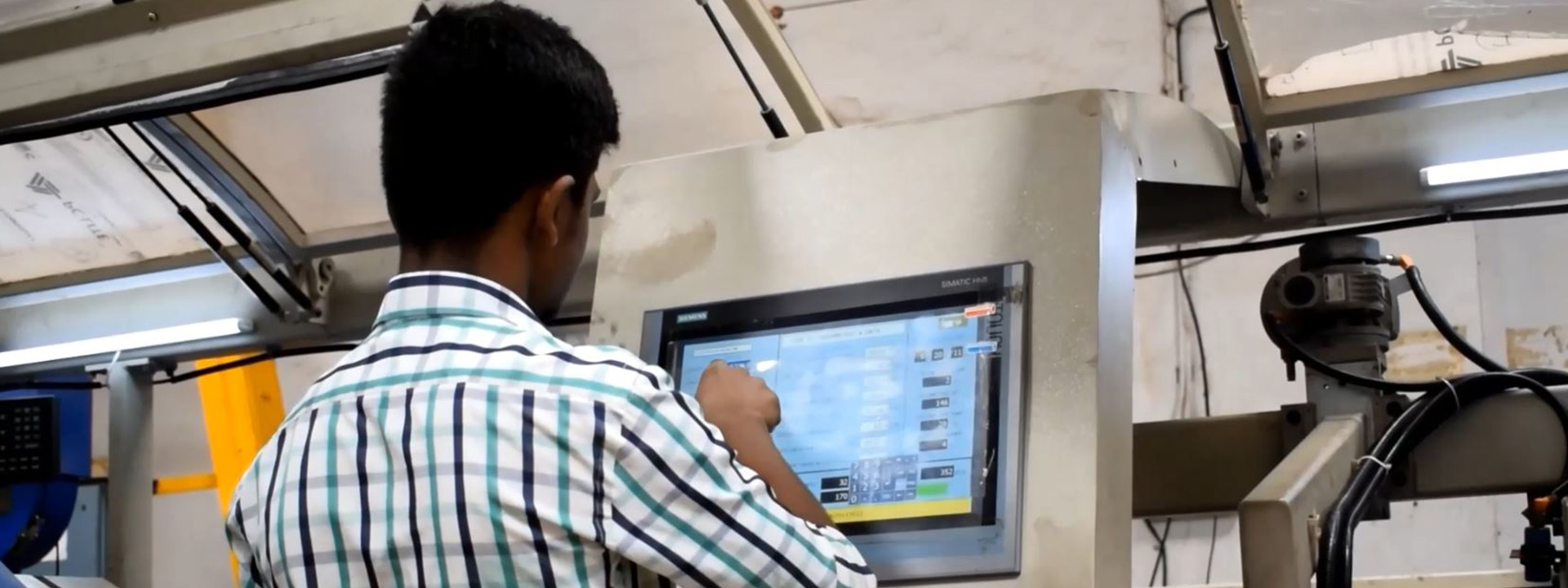
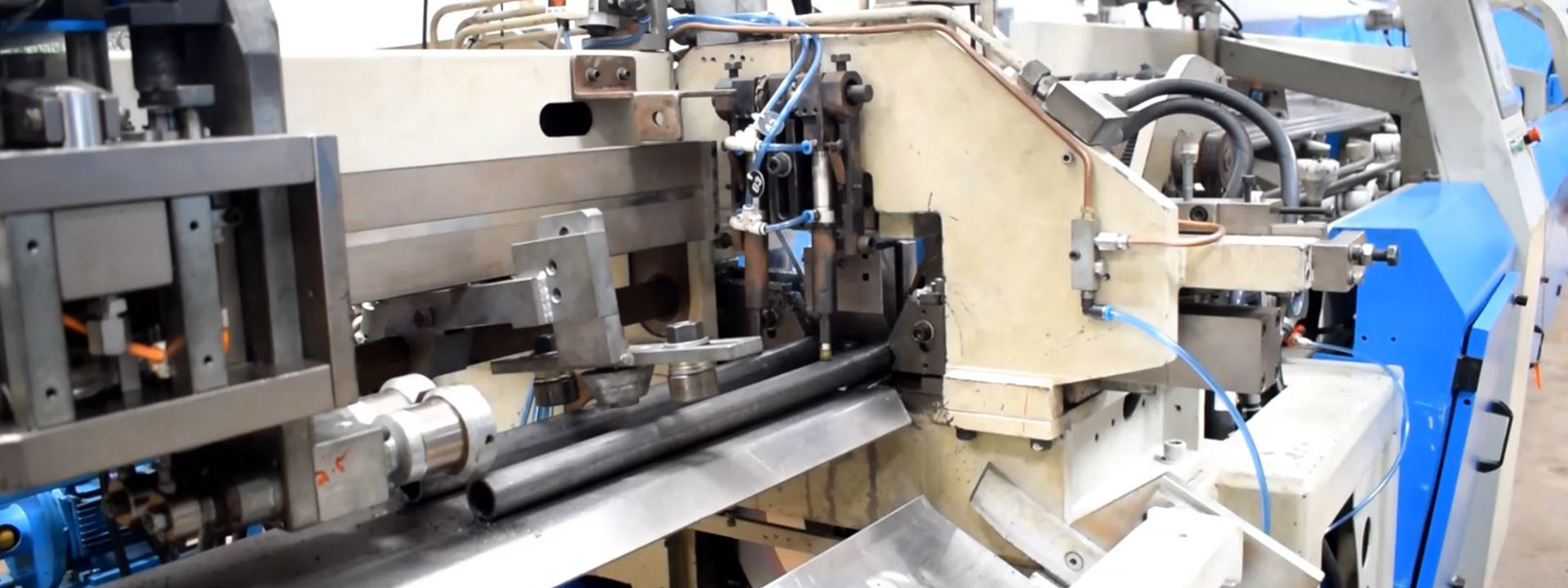
Tube Cutting Machine
- High speed Twin Tube Cutting & Deburring / Chamfering Machine
- High speed Dual Shear Cutting Machine
- Semi-automatic Tube Cutting and Facing / Chamfering Machine
High Speed Twin Tube Cutting Deburring / Chamfering Machine
- Completely Automated machine
- Precise speed control Sewing
- Highly effective six point Tube Clamping > Tube diameter range: 15 mm to 70 mm
- Tube thickness range: 1.2 mm to 5 mm
- Cut to length accuracy of +/- 0.4 mm
- Tubes with material strength up to 500 MPa
- Quickly settable cutting parameters with interactive interface
- QCO & IIOT enabled
- Optional add-ons
- Tube Deburring or Chamfering units
High Speed Dual Shear Cutting Machine
- Burr Free Cutting Edge
- Higher Productivity process
- Suitable for Carbon Steel
- Tube Range: Dia 50 to 100 mm
- Tube Thickness: 1.5 to 6 mm max
- Length control + / -0.5 mm
- Precision speed control
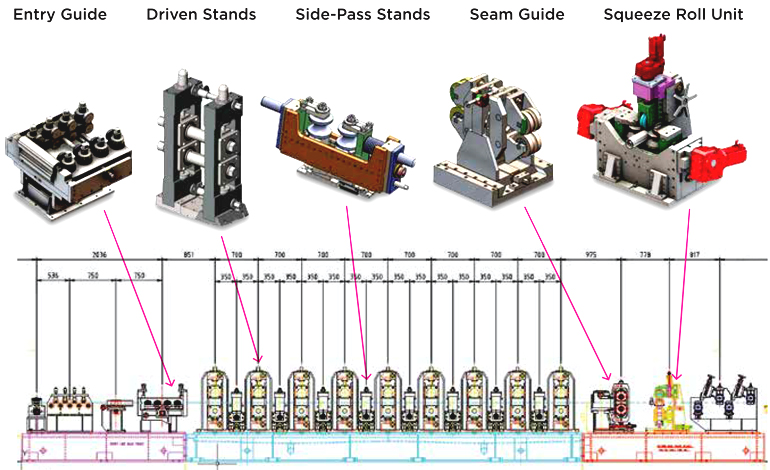
Squeeze roll with servo system
- Servo controlled system with setup recall provision, thereby ensuring repeatablity & reliability by eliminating operator intervention
- Extended Bea ring life
- Reduced weld related defects and ensures consistency in forge line due to precise position control
- SG Iron Casting stands for better shock absorption and stability
- Stand Clamping system with quick change over
- Tube Mill for all form of specialized tubing.
- Rigid Mill construction to produce tubes of carbon steel & high strength steel with diameter/thickness ratio upto 7.
- We also supply individual elements to upgrade the existing tube mill.
- Entry line—Accumulator—Forming Stands—Squeeze rolls—Flying Cutoff—Online Chamfering.
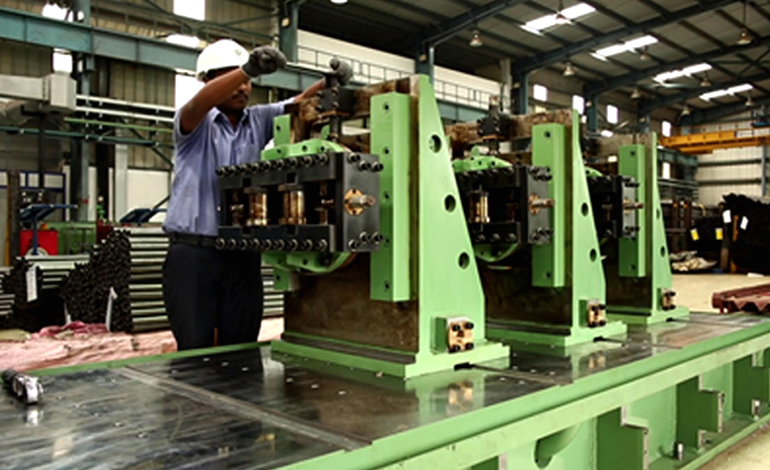
With the latest’s development in power electronics the Longitudinally welded tube is manufactured by high frequency induction welding. A typical high productive setup consists of following elements
- Double Decoiler
- Automatic strip end joiner
- Accumulator
- Forming stands
- Finpass stands
- High frequency induction welder
- Squeeze roll
- OD bead remover
- Cooling chamber
- Sizing section
- Turk heads
- Flying cut off
- Runout table
To achieve the productivity and quality TIMB designs and manufactures the appropriate equipment for the carbon steel and stainless-steel tube industry from the smallest diameter of 10 mm to the biggest of 250 mm, with wall thicknesses of 0.5 to 16.0 mm in carbon-steel, stainless steel, aluminum, brass- and copper/-alloys and in different qualities.
Based on an intelligent modular design the individual machines can be combined to production lines for mass production – also fully automated and customized.
In-house production is carried out with a high production depth and according to the latest manufacturing methods with strictest quality standards. Here, engineers, designers, the production team and automation experts work seamlessly together – coordinated internally and externally by a project manager. This makes teamwork easier and prevents communication deficits.
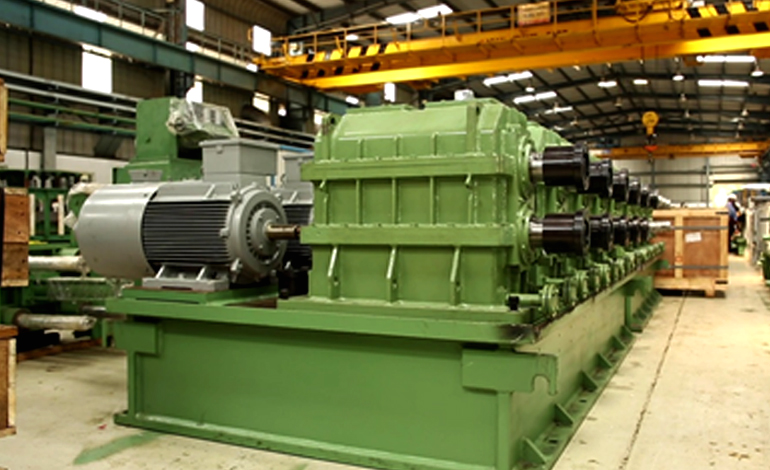
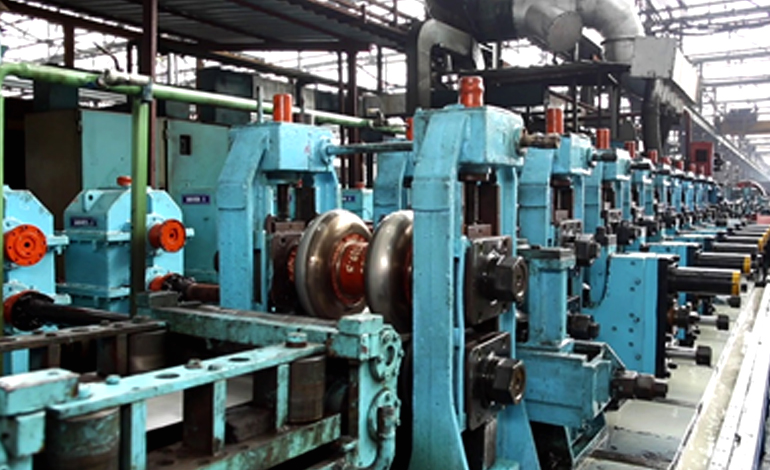
Customers count on our machine for the following advantages
- High productivity and availability
- Reliable reproducibility
- Short set-up times
- Simple operation
- Increased process stability
- Continuous production
- Automated processes
- Individual visualization